The Charm of Seraya Timur Handwoven Fabrics: Nature's Touch from Secang Wood to Pomegranate Peel
In Seraya Timur Village, located at the easternmost part of Karangasem District, Karangasem Regency, Bali, the traditional weaving craft is well-known. To this day, the process of creating woven fabrics in this village still relies on natural materials as dyes, making it particularly appealing to researchers and textile craft enthusiasts, especially with the use of materials like Secang Wood, Pomegranate Peel, and Indigo Leaves.
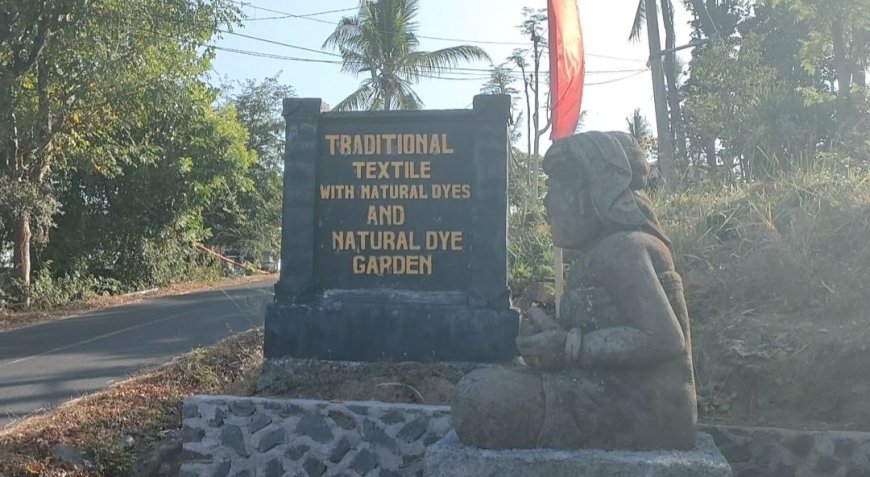
Textile Crafts and Their Relation to Fabric as a Core Material
Fabric produced through weaving processes holds high artistic and economic value due to the time-consuming series of steps involved. As we know, textiles encompass various types of fabrics created through methods like weaving, tying, and pressing, with the aim of producing market-ready products. The process begins with selecting fibers, which are then spun into long threads to be woven or knitted, resulting in high-quality fabric.
In Indonesia, weaving has become a cultural heritage passed down through generations in various weaving-producing regions. Each area features distinctive motifs and techniques, reflecting the local cultural identity. Woven fabrics are sought after by many due to their shapes, colors, motifs, and the uniqueness of their production process, including the use of traditional looms and natural dyes.
Karya Sari Warna Alam Group (Photo Source: Personal Collection)
According to Poppy, the manager of the woven fabric business "Karya Sari Warna Alam" in Seraya Timur Village, the fabric production process in this area relies entirely on natural materials. The dyeing of threads, boiling of fabrics, and drying processes are carried out traditionally, utilizing surrounding natural resources, including sunlight. Natural dyes are obtained from locally cultivated plants, enhancing the uniqueness of Kain Tenun Bebali, the name for this region’s traditional fabric.
Gate to the Woven Fabric Business in Seraya Village (Photo Source: Personal Collection)
Natural Dye Materials
The fabric dyeing process in Seraya Timur Village utilizes various natural ingredients derived from local plants, such as roots, leaves, fruits, and tree bark. Below are the natural dye materials used:
-
Indigo Leaves (Tarum)
The Indigofera tinctoria plant, or commonly known as tarum, has been used for centuries as a source of natural blue dye. Fresh leaves are soaked in water to start a fermentation process that produces a thick blue liquid. This liquid is then used to dye threads, creating a distinctive and long-lasting blue color. This natural dye is widely used in traditional fabric production such as batik and woven textiles.Indigo Leaves (Photo Source: Personal Collection)
-
Areca Nut
The Areca catechu tree offers not only cultural significance but also practical uses. Its ripe fruit, especially those with wrinkled skin, is boiled to produce a natural cream color. This color is often used as a base dye or mixed with other colors to create soft gradations in traditional fabrics. -
Noni Root
The bark of the Morinda citrifolia plant root is known as a source of natural red dye. Its carotenoid content provides a strong red hue after boiling. This color is often used in traditional fabrics, offering a warm and bold tone that is long-lasting. Moreover, noni is valued in traditional medicine. -
Pomegranate Peel
The peel of Punica granatum fruit contains high tannin levels, making it ideal for producing a natural yellow color. Boiling the peel for 2-3 hours ensures a rich yellow hue, which can be combined with blue dye to create natural green shades commonly used in traditional textiles. -
Sidawayah Flowers
Woodfordia floribunda flowers are unique natural dye materials capable of producing brown and black hues. Black dyeing involves boiling threads previously dyed blue with these flowers. The resulting dark color gives an elegant impression often used in specific motifs. -
Sappanwood
Caesalpinia sappan wood is a popular natural dye source for creating pink shades. Repeated dyeing processes can achieve the desired intensity. Apart from dyeing fabric, sappanwood extract is known in the herbal world as a healthy traditional drink ingredient. -
Lime
Lime plays a crucial role as a supporting material in natural dyeing processes. In indigo leaf fermentation and noni root boiling, lime accelerates the chemical reactions that produce deep blue and red colors. Additionally, lime helps form dye pastes, making them easier to apply to threads or fabrics.Production Area of Karya Sari Warna Alam (Photo Source: Personal Collection)
Tools and Process Steps
The production of woven fabrics using natural dyes employs simple tools such as basins, large pots, mortars as traditional pounding tools, jars for soaking, sieves, blenders to speed up dissolution processes, and cement tanks for storing dye liquids. Each tool has a specific function, such as large pots for boiling dye materials to extract their natural pigments and jars for soaking threads in dye liquids to achieve the desired colors.
Washing Indigo Leaves (Photo Source: Personal Collection)
The image above shows the process of washing and squeezing indigo leaves, which will later be boiled using firewood as the primary heat source. The washing stage is done 3-5 times to remove any dirt still clinging to the leaves, ensuring they are ready for further processing. All primary materials for natural dyes, including indigo leaves, are sourced from local residents' fields cultivated to preserve the quality of natural-dyed textiles.
Boiling Natural Dye Paste with Firewood (Photo Source: Personal Collection)
Afterward, threads are dipped into the dye liquid multiple times to reach the desired color intensity, followed by rinsing to remove any excess dye. The dipping process is adjusted to the desired color consistency of the thread, which will then be woven into beautiful fabric. The final step involves drying the dyed threads under sunlight to allow the color to dry and adhere firmly to the thread fibers, preparing them for the next weaving process.
Drying Fabric Under Sunlight (Photo Source: Personal Collection)
Once the threads are dried to the desired color, they are tied in certain areas to create unique motifs before being dipped again in dye baths to create gradients. After the dyeing process, the threads are ready for weaving, producing fabrics with various unique motifs and colors that reflect the cultural heritage of Seraya Timur Village.
Finished Fabric Ready for Weaving (Photo Source: Personal Collection)
The dyed threads are then woven, often done by local villagers at their homes before being collected by the Karya Sari Warna Alam group for sale. The woven fabrics from Seraya Timur Village have gained international recognition and have been showcased at events like the Bali Arts Festival held in Denpasar City. The woven fabrics of Seraya Timur Village not only symbolize Indonesia’s cultural richness but also serve as high-art-value products that continue to be in demand locally and internationally.